Everything You Need to Know About Quenching Oil Centrifugal Filtration Machine
Quenching oil centrifugal filtration machine are an essential part of the manufacturing industry. They are used to cool and harden parts that have been exposed to high temperatures or stress. By using a quenching oil centrifugal machine, you can reduce the risk of breakage and ensure that the parts you produce are as strong and durable as possible. In this blog post, we will take a look at everything you need to know about quenching oil centrifugal machines, including how they work, the different types available, and the safety procedures that should be followed when using one.
Which oil is used for quenching ?
Quenching is a process of heating and cooling a material to harden its surface. The oil used for quenching can be mineral-based or synthetic. Mineral-based oils, such as those manufactured by CBSEnergy, are composed of hydrocarbons and other components that provide excellent heat transfer and fast cooling rates. Synthetic quench oils are formulated with polymers and other compounds to provide superior lubricity, thermal stability, and water resistance. Regardless of which type of oil is used, it is important to select an oil with a viscosity suited for the application.
Which gas is used for quenching ?
Quenching is a process used to harden the metal and involves submerging the metal into a liquid, typically oil or water. Depending on the desired result, a gas such as nitrogen, argon, hydrogen, or carbon dioxide can be used instead. Using gas is a form of quenching known as gas quenching and is one of the most effective ways to rapidly cool the metal while retaining the desired hardness. At CBSenergy, we use nitrogen gas to quench, as it offers greater cooling power and is non-combustible. Nitrogen gas also helps reduce distortion when compared to traditional quenching methods. This is because the rapid cooling causes minimal thermal shock, thus reducing any potential warping of the material. At Cbsenergy, all of our quenching processes are regularly monitored to ensure they are performed at the highest quality standard possible.Â
Our staff has extensive knowledge and experience in this field, allowing us to adjust our machines to provide an optimal outcome for each product. With Cbsenergy’s expertise and quality machines, customers are assured that their products will come out with an enhanced surface finish and improved mechanical properties. We proudly offer a wide variety of quenching services for different materials ranging from steel to plastic products. Cbsenergy prides itself on offering efficient and cost-effective solutions for each customer’s specific needs. Through our technology and reliable services, we strive to exceed customer expectations every time.
Which quenching method is the most commonly used ?
Quenching is an important heat treatment process used to harden and strengthen a variety of metals and alloys. There are several different quenching methods, but the most commonly used method is oil quenching. Oil quenching involves submerging heated metal into a liquid bath of oil at a certain temperature to rapidly cool it. This method is preferred over the air or water quenching because it provides more uniform cooling and reduces the risk of warping or cracking from thermal shock. The oil also acts as a lubricant, which can help prevent scaling and improve the overall finish of the metal.Â
Quenching Oil centrifugal filtration machine use high-velocity jets of pressurized quenching oil to rapidly cool metal components. These machines typically operate under high temperatures and pressure to reach the desired temperature quickly without inducing thermal shock. The quenching oil centrifugal filtration machine uses a high-speed rotation impeller to disperse the oil across the surface of the metal to achieve optimal cooling. In addition, this machine uses carefully-controlled heating elements to ensure the desired cooling rate and minimize any distortion in the metal’s shape due to uneven cooling.
Can you reuse oil after quenching ?
The answer to this question is a bit more complicated than a simple yes or no. In general, most quenching oils can be reused for multiple applications if it is adequately filtered. However, the effectiveness of the quench will decrease with each successive use. Therefore, the recommendation is that you should replace the oil if the temperature or viscosity readings fall outside the specified parameters. It’s also important to ensure that the oil is free of contaminants or debris as these can cause damage to components during heat treatment. If you are unsure of how to properly filter and store your quenching oil, consult with an experienced heat treatment specialist before attempting to reuse it.
What is cold quenching oil ?
Cold quenching oil is a type of quenching oil used to cool down metal materials rapidly. It is usually composed of a base oil blended with additives that offer lubricity and corrosion protection properties. Cold quenching oil works by transferring heat quickly away from the metal during the quenching process, resulting in a much harder and stronger material.Â
Unlike hot quenching oils, cold quenching oils have a lower viscosity, meaning they are thinner and easier to use than their hot counterparts. Additionally, the lower temperatures used with cold quenching oils allow for higher mechanical strength and less dimensional change in the metal material. This makes cold quenching oils ideal for applications that require high-strength parts without deforming them in the process.Â
Cold quenching oils can also be recycled after use, saving costs associated with disposal and providing a more environmentally friendly option compared to other quenching methods.Â
The main benefit of using cold quenching oil is that it offers superior hardness and strength properties when compared to hot quenching oils. Cold quenching oils can also be recycled after use, which reduces costs associated with disposal and offers a more environmentally friendly option than other quenching methods. For these reasons, cold quenching oil is often preferred over hot quenching oil for many applications.
What temperature should quenching oil be ?
Quenching oil must be heated to the right temperature to ensure proper heat transfer and optimal results. The temperature of the quenching oil is typically between 180°F to 400°F (82°C to 204°C). When selecting a quenching oil, it is important to note the maximum recommended temperature for that oil, as some are designed for higher temperatures than others. It is also important to keep an eye on the temperature of the quenching oil during the quenching process, as it will gradually cool over time. Quenching oil should not exceed its maximum temperature recommendation or else it may cause damage to the metal being treated.
How long does quenching oil last ?
Quenching oil can last for a long time if it is used and stored correctly. It should be kept in a cool, dry place away from direct sunlight and moisture. Quenching oil usually has an expected shelf life of at least 2 years, though some companies may have different shelf life estimates based on the type of oil they use.
When the oil is in use, it is subject to degradation due to heat and oxidation. The rate at which this happens depends on the temperature and the type of metal being quenched. For example, steel quenching requires a higher temperature and therefore the oil will degrade faster. If you are using a quenching oil centrifugal machine, the oil can be recycled and reused multiple times before needing to be replaced. This extends the life of the quenching oil significantly and reduces costs associated with purchasing new oil.
What is the process of quenching ?
Quenching is a heat treatment process that involves rapidly cooling a material to induce hardening. It is an important technique used in metallurgy to produce durable and strong metal components that can withstand harsh environments. The quenching process involves heating the metal to a certain temperature and then rapidly cooling it with a quenching medium such as oil, water, or air. This rapid cooling causes the metal to become much harder than it would otherwise be, resulting in greater strength and improved wear resistance.
During quenching, the heated metal is placed in the quenching medium and the temperature is lowered quickly. The quenching medium is selected based on the type of material being quenched and the desired result. For example, some materials may require an oil quench while others may need a water quench. When done correctly, the process can result in a strong and durable finished product.
Using a centrifugal machine for quenching is becoming increasingly popular because it can provide a more consistent cooling rate and reduce the risk of cracking or warping due to uneven cooling. The centrifugal force generated by the machine helps to evenly distribute the heat throughout the material and can reduce distortion caused by the cooling process. Additionally, the machine can also reduce waste since it allows for shorter cooling times and more efficient use of the quenching medium.
What are the benefits of using a quenching oil Centrifugal Filtration Machine ?
Quenching oil centrifugal filtration machines offer a range of benefits for metalworking operations. These include improved safety, increased productivity, and better control over the quenching process.
The use of a quenching oil centrifugal filtration machine can reduce the risk of fire and other accidents, as the quenching oil is automatically circulated and filtered in a closed system. This also helps to extend the life of the quenching oil and reduce waste.
The use of a quenching oil centrifugal filtration machine also increases productivity, as the machine can heat up oil quickly, allowing for faster quenching times. It also provides greater control over the quenching process, allowing for more consistent results.Â
Finally, quenching oil centrifugal filtration machines can improve the quality of the product, as they provide a more uniform temperature across all parts. This ensures that all parts are quenched evenly and effectively.
Overall, the use of a quenching oil centrifugal machine offers numerous benefits to metalworking operations, including improved safety, increased productivity, better control over the quenching process, and improved product quality.
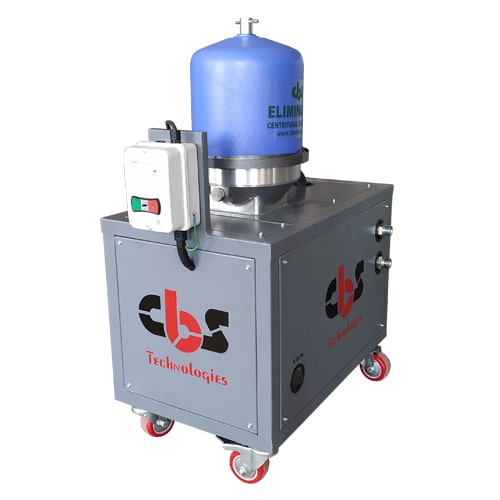
What is the Viscosity of Quench oil ?
Viscosity is an important factor to consider when choosing a quench oil. Quench oil is designed to cool parts quickly and efficiently, and the viscosity of the oil plays a role in its cooling rate. The viscosity of quench oil refers to how thick it is and can be measured in centistokes (CST).Â
The lower the viscosity, the thinner the oil and the faster it can cool a hot part. Generally, low-viscosity quench oils are best suited for small parts that need to be cooled quickly. High-viscosity quench oils are better for large parts or for parts with intricate geometries that require a slower cooling rate.Â
The most common quench oils range in viscosity from 65-100 CST. If a quenching oil falls outside of this range, it may not be suitable for the application at hand. It is important to note that some quench oils are formulated with additives such as anti-foaming agents, corrosion inhibitors, and anti-rust agents that can affect their viscosity.Â
When selecting a quench oil, it is important to make sure that the viscosity is appropriate for your application. If you are unsure of what quench oil is right for you, consult a professional to ensure you get the best performance from your quenching process.
What is quench pressure ?
Quench pressure is the pressure applied to the surface of a metal being quenched. This pressure helps to accelerate the cooling process, resulting in a stronger and more durable metal. It also helps to minimize distortions and warping that can occur with the quenching process.
Quench pressure is usually determined by the material being quenched, as different materials have different requirements for quench pressure. Generally, softer metals require less quench pressure than harder metals. It is important to note that too much quench pressure can cause cracking and other damage to the metal, while too little quench pressure can result in a weaker metal. It is important to find the right balance between quench pressure and cooling rate to get the desired results.
In some cases, special equipment such as quench tanks or quench presses is used to apply the necessary quench pressure. These tools help to maintain a consistent pressure level and help to avoid any damage from over-pressuring the material.
Ultimately, quench pressure is an important factor in the overall success of the quenching process and must be taken into consideration when choosing the right quenching medium and method.
What are the 4 Main Quenching mediums used to quench steel ?
The four main quenching mediums used to quench steel are water, oil, air, and polymers. Each has its pros and cons, but all are capable of producing the desired result – the hardening of a steel object using rapid cooling.
Water quenching is often the most cost-effective and widely used quenching medium, due to its lower cost and high heat transfer rate. It is often used in industrial applications, however, it can cause cracking and distortion in some materials if it cools them too quickly.
Oil quenching is another popular choice for industrial use. Oil cools more slowly than water, making it ideal for thinner or more complex pieces of steel. It also doesn’t cause as much distortion in materials as water does. The downside is that oil is more expensive than water and can become flammable when heated.
Air quenching is used when the speed of cooling is an issue, but with it comes a high risk of warping and other imperfections in the material due to its low heat transfer rate. It is best used for simpler pieces with minimal detail or thicker pieces that require a faster quench.
Polymer quenching is similar to air quenching in terms of speed and risk of warping, however, it has less of a risk of oxidation due to its higher viscosity. It is often used when treating more delicate items like medical equipment or jewelry.
Which is the fastest quench medium?
The fastest quench medium for steel depends on several factors, such as the type of steel, size and shape of the workpiece, and the required final hardness. Generally speaking, water is the fastest quench medium and is ideal for hardening carbon steels and alloy steels with high carbon content. Oil is also a popular quench medium, but it is slower than water, making it suitable for steel with lower carbon content or parts that have complex shapes. Forced-air quenching can be used to quickly harden steel, but requires special equipment and is limited to small parts that can fit in the air stream. Vacuum furnaces are another option and can provide fast cooling rates while minimizing distortion and cracking.
What is a quench unit?
A quench unit, also known as a quenching oil Centrifugal Machine, is a device used for the rapid cooling of metal parts. It is widely used in many industries including automotive, aerospace and defense. The quench unit works by rapidly circulating hot oil around the metal parts to draw away their heat and bring them to a desirable temperature quickly. This process is called quenching. Quench units from CBSenergy are designed to provide reliable, efficient and consistent cooling results every time. They are perfect for use in a variety of applications, from hardening and tempering to stress relief.
How do I Choose the right quenching oil Centrifugal Machine for my needs?
Choosing the right quenching oil Centrifugal Machine can be a difficult task, but with the right advice, you can make an informed decision. To make sure you get the best machine for your needs, consider the following points:
- Capacity: Make sure to consider the capacity of the quenching oil centrifugal machine, in terms of volume and speed. Depending on the size of your production line and the type of material you will be quenching, a smaller or larger centrifuge may be needed.
- Quality: It is important to purchase a machine that is made of high-quality components, so it can withstand high temperatures and pressure. Look for machines from reputable brands like CBSenergy that provide quality assurance and customer service.
- Efficiency: Check the energy efficiency rating of the centrifuge, as this will tell you how much electricity it will use and how efficient it is. The higher the rating, the more money you can save in the long run.
- Safety: Make sure to check all safety measures such as emergency shut-off features, control panel design, and safety-rated components. Ensuring a safe working environment is essential for any industry.
- Maintenance: Regular maintenance is key for optimal performance and cost savings, so choose a machine with easily accessible parts and services that are covered by warranty.
By considering these factors, you can find the perfect Quenching oil Centrifugal Filtration Machine for your needs. Remember to do your research and always consult with professionals before making a purchase.
What is quenching fluid?
Quenching fluid is a cooling medium used during the process of quenching metal. It helps to control the rate of cooling to obtain the desired result. Quenching fluids are designed to quickly remove heat from metal by transferring it away from the part and into the surrounding environment.
Quenching fluids can be classified into four main categories: water, oil, gas, and air. Each type has its unique properties and characteristics, making them suitable for different applications and materials. Water is typically used for low-carbon steel parts, while oil is often preferred for higher-carbon steels. Air or gas can be used for high-temperature quenching, as well as for high-alloy steels.Â
Quenching fluids must be carefully selected depending on the material being quenched and the desired outcome. They should also be monitored closely to ensure that they remain within safe temperature ranges and that proper concentrations are maintained. When using quenching fluids, safety precautions should always be taken to prevent accidental contact with skin or eyes.
What is the principle of quenching?
The principle of quenching is to quickly cool a hot metal object, such as a metal part or alloy, so that the material changes from an austenitic to a martensitic structure. This is done to harden or strengthen the metal or alloy. Quenching is accomplished by immersing the hot metal in a liquid medium, typically oil or water. Quenching oil is often used for faster cooling and better surface protection, as it can absorb more heat than water. In particular, CBSenergy quenching oil is widely used as it has been proven to reduce quench time while providing superior protection and uniform cooling of the surface. A centrifugal machine uses this oil to evenly coat parts with a thin layer of oil before placing them into a furnace for heating.
After heating, the parts are placed into the centrifuge chamber which spins at high speed, thus coating each piece with the same layer of quenching oil. When parts are placed into the bath after being heated, they are brought up to temperature very quickly due to the combination of thermal conduction and convection. The rotating action also helps distribute the heat more evenly over each piece which reduces the chances of warping or other deformation issues. The use of centrifuges also eliminates splashing and dripping during quenching which can be hazardous if done without proper precautions. As well, centrifuges enable parts to reach a consistent hardness all over due to the even application of quenching oil on each piece.
Why is water used in quenching?
Quenching is a process used to strengthen and harden metals such as steel. It typically entails heating the metal to a specific degree before cooling it down. Water is the most commonly used medium for quenching because it can cool metal extremely quickly and effectively. Quenching with water also helps reduce the risk of cracking or warping due to thermal shock.
Water has a relatively low specific heat capacity and high thermal conductivity compared to other liquids, making it very effective at cooling hot metals. When the heated metal is placed in the water, the molecules within the water absorb the heat from the metal, thus cooling it. This process is known as quenching.
The rate of cooling depends on the temperature of the water and the volume of water used. For example, if you are quenching a small object, using cold water will cool it faster than using warm water.
It is important to remember that water can also cause warping and distortion when quenching. To avoid this, it is recommended that the water is agitated to create turbulence around the heated object, helping to distribute the heat more evenly. If you are not familiar with this process, it is best to consult a professional before attempting quenching with water.
What is called quenching?
Quenching is a process of heat treatment, which is used to change the properties of a material. This process involves heating the material to a specific temperature and then rapidly cooling it with water, oil, air, or other fluids. The rapid cooling hardens the material and results in increased strength and improved resistance to wear and tear. Quenching can also be used to create special qualities in materials such as corrosion resistance and wear resistance. Quenching is commonly used in metallurgy and engineering applications to improve the mechanical properties of metals such as strength, hardness, ductility, and toughness.
What are the types of quenching?
When it comes to quenching, several different types can be employed to achieve the desired result. The most common type of quenching is oil quenching, which involves submerging the workpiece in oil or a mix of oil and other fluids. This type of quenching produces a hard, brittle surface layer on the workpiece. Oil quenching is often used for high-carbon steel and can be used for other materials such as aluminum and brass.
Another type of quenching is air quenching. This type of quenching does not involve submerging the workpiece in any liquid but instead uses forced air to cool the part. Air quenching can be used with low-carbon steels and is often used for more complex parts.
Water quenching is another type of quenching, and involves submerging the workpiece in water. This type of quenching results in a less hard, more ductile surface layer on the workpiece. Water quenching is often used for ferrous alloys and some non-ferrous alloys such as aluminum and brass.
The last type of quenching is cryogenic quenching, which involves cooling the workpiece with liquid nitrogen. Cryogenic quenching produces an extremely hard and brittle surface layer on the workpiece. It is often used for low-alloy steels and certain stainless steels.
What are the three Stages of quenching?
Quenching is the process of quickly cooling a material so that it acquires certain properties. This process consists of three distinct stages: austenitizing, quenching, and tempering.
The first stage is called austenitizing. During this process, the material is heated up to temperatures around 900–1400°F (480–760°C). Depending on the type of steel, the temperature range may be higher or lower. The heat brings about a transformation of the structure of the material so that its structure becomes austenitic. This structure can be very hard and strong but is also quite brittle.
Once the material is brought to the proper temperature, it must be quickly cooled to retain the desired properties. This process is called quenching and usually involves immersing the material in a medium such as oil, water, or even air. The choice of medium depends on what type of steel is being used and how it needs to be cooled.
The last step is tempering, which reduces the brittleness of the material caused by the austenitizing and quenching steps. Tempering is done by heating the steel again but at much lower temperatures than before. This allows for some of the hardness to be reduced while maintaining the strength and other desirable properties that were acquired during the earlier stages. The exact temperature range and time will depend on what properties are desired from the final product.
By going through these three stages, quenching can produce a material with several desirable properties. It can create materials that are hard, strong, wear-resistant, and more able to withstand high temperatures. It is important to understand these stages and their effects when deciding what type of quenching process is right for any given application.
Conclusion
Quenching oil centrifugal filtration machine are essential pieces of equipment for many industries, from automotive to industrial manufacturing. They provide a safe, effective and economical way to quickly cool parts, helping you produce superior results. When it comes to selecting the right quenching oil centrifugal machine for your needs, it is important to understand the principles of quenching and how to choose the best option for your requirements. By considering the three stages of quenching, you can make sure that your machine will be able to handle the workload and produce the desired results.